STEP 1. Using scan tool (M.U.T-III), diagnose the CAN bus line.
(1) caution | To prevent damage to scan tool (M.U.T-III), always turn the power supply mode of the engine switch to the OFF position before connecting or disconnecting scan tool (M.U.T-III). |
Connect scan tool (M.U.T-III). Refer to "How to connect scan tool (M.U.T.-III)

."
(2) Turn the power supply mode of the engine switch to ON.
(3) Diagnose the CAN bus line.
(4) Turn the power supply mode of the engine switch to OFF.
Is the CAN bus line found to be normal?
Go to Step 2
.
Repair the CAN bus line (Refer to GROUP 54C, Diagnosis
).
STEP 2. Using scan tool (M.U.T.-III), read the diagnostic trouble code.
(1) caution | To prevent damage to scan tool (M.U.T.-III), always turn the power supply mode of the engine switch to the OFF position before connecting or disconnecting scan tool (M.U.T.-III). |
Connect scan tool (M.U.T.-III). Refer to "How to connect scan tool (M.U.T.-III)

."
(2) Turn the power supply mode of the engine switch to ON.
(3) Check if OSS-ECU DTC B1133 is stored.
(4) Turn the power supply mode of the engine switch to OFF.
Is the DTC stored?
Refer to diagnostic trouble code chart
.
Go to Step 3
.
STEP 3. Using scan tool (M.U.T.-III), check data list.
(1) caution | To prevent damage to scan tool (M.U.T.-III), always turn the power supply mode of the engine switch to the OFF position before connecting or disconnecting scan tool (M.U.T.-III). |
Connect scan tool (M.U.T.-III). Refer to "How to connect the Scan Tool (M.U.T.-III)

."
(2) Turn the power supply mode of the engine switch to OFF.
(3) Operate the engine switch to change the power supply mode, and check that the data list display of ETACS-ECU is changed.- When power supply mode is ACC or ON.
| ETACS-ECU data list | Item No. | Item name | Normal condition | 29 | Ignition switch(ACC) | ON |
|
- When power supply mode is ON or START.
| ETACS-ECU data list | Item No. | Item name | Normal condition | 30 | Ignition switch(IG1) | ON |
|
- When power supply mode is ON.
| ETACS-ECU data list | Item No. | Item name | Normal condition | 44 | Ignition switch(IG2) | ON |
|
OK: Normal conditions are displayed for all the items.
Are the check result normal?
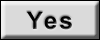
(Normal conditions are displayed for all the items.) :
Go to Step 4
.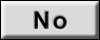
(Normal condition is not displayed for item No. 29.) :
Go to Step 6
.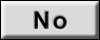
(Normal condition is not displayed for item No. 30.) :
Go to Step 13
.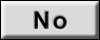
(Normal condition is not displayed for item No. 44.) :
Go to Step 19
.
STEP 4. Using scan tool (M.U.T.-III), check data list.
(1) caution | To prevent damage to scan tool (M.U.T.-III), always turn the power supply mode of the engine switch to the OFF position before connecting or disconnecting scan tool (M.U.T.-III). |
Connect scan tool (M.U.T.-III). Refer to "How to connect the Scan Tool (M.U.T.-III)

."
(2) Turn the power supply mode of the engine switch to OFF.
(3) Check the OSS-ECU data list. | Item No. | Check item | Power supply mode | Display | 16 | IG2 output (monitor) | IG-ON | ON | Other than IG-ON | OFF |
|
OK: Depending on the state of power supply mode, the display is turned ON/OFF.
Is the check result normal?
Go to Step 27
.
Go to Step 5
.
STEP 5. Check of short and open circuit in IG2M line between OSS-ECU connector and IG2 relay connector
STEP 7. Resistance measurement at ACC relay connector (ground line)
(1) Disconnect the connector, and measure at the wiring harness side.
(2) Measure the resistance between the ACC relay connector (ground line) and the body ground.OK: Continuity exists (2 Ω or less)
Is the check result normal?
Go to Step 9
.
Go to Step 8
.
STEP 8. Check of open circuit in ground line between the ACC relay connector and the body ground
STEP 9. Voltage measurement at ACC relay connector (ACC line).
(1) Disconnect the connector, and measure at the wiring harness side.
(2) Measure the voltage between the ACC relay connector (ACC line) and the body ground.OK: System voltage
Is the check result normal?
Go to Step 11
.
Go to Step 10
.
STEP 10. Check of short and open circuit in ACC line between the OSS-ECU connector and the ACC relay connector
Is the check result normal?
Replace the OSS-ECU.
Repair the connector(s) or wiring harness.
STEP 11. Check of short and open circuit in power supply line between the junction block connector and the ACC relay connector
STEP 12. Voltage measurement at ETACS-ECU connector (ACCI line).
(1) Turn the engine switch from "LOCK" (OFF) position to "ON" position.
(2) Disconnect the connector, and measure at the wiring harness side.
(3) Measure the voltage between the ETACS-ECU connector (ACCI line) and the body ground.OK: System voltage
Is the check result normal?
Go to Step 26
.
Repair the wiring harness, ACCI line between the ETACS-ECU connector and the fusible link.
STEP 14. Resistance measurement at IG1 relay connector (ground line)
(1) Disconnect the connector, and measure at the wiring harness side.
(2) Measure the resistance between the IG1 relay connector (ground line) and the body ground.OK: Continuity exists (2 Ω or less)
Is the check result normal?
Go to Step 16
.
Go to Step 15
.
STEP 15. Check of open circuit in ground line between the IG1 relay connector and the body ground
STEP 16. Voltage measurement at IG1 relay connector (IG1 line).
(1) Disconnect the connector, and measure at the wiring harness side.
(2) Measure the voltage between the IG1 relay connector (IG1 line) and the body ground.OK: System voltage
Is the check result normal?
Go to Step 18
.
Go to Step 17
.
STEP 17. Check of short and open circuit in IG1 line between the OSS-ECU connector and the IG1 relay connector
Is the check result normal?
Replace the OSS-ECU.
Repair the connector(s) or wiring harness.
STEP 18. Voltage measurement at combination meter connector (IG1 line).
(1) Turn the engine switch from "LOCK" (OFF) position to "ON" position.
(2) Disconnect the connector, and measure at the wiring harness side.
(3) Measure the voltage between the combination meter connector (IG1 line) and the body ground.OK: System voltage
Is the check result normal?
Go to Step 26
.
Repair the wiring harness, IG1 line between the combination meter connector and the fusible link.
STEP 20. Resistance measurement at IG2 relay connector (ground line)
(1) Disconnect the connector, and measure at the wiring harness side.
(2) Measure the resistance between the IG2 relay connector (ground line) and the body ground.OK: Continuity exists (2 Ω or less)
Is the check result normal?
Go to Step 22
.
Go to Step 21
.
STEP 21. Check of open circuit in ground line between the IG2 relay connector and the body ground
STEP 22. Voltage measurement at IG2 relay connector (IG2 line).
(1) Disconnect the connector, and measure at the wiring harness side.
(2) Measure the voltage between the IG2 relay connector (IG2 line) and the body ground.OK: System voltage
Is the check result normal?
Go to Step 24
.
Go to Step 23
.
STEP 23. Check of short and open circuit in IG2 line between the OSS-ECU connector and the IG2 relay connector
Is the check result normal?
Replace the OSS-ECU.
Repair the connector(s) or wiring harness.
STEP 24. Check of short and open circuit in power supply line between the junction block connector and the IG2 relay connector
STEP 25. Voltage measurement at ETACS-ECU connector (IG2 line).
(1) Turn the engine switch from "LOCK" (OFF) position to "ON" position.
(2) Disconnect the connector, and measure at the wiring harness side.
(3) Measure the voltage between the ETACS-ECU connector (IG2 line) and the body ground.OK: System voltage
Is the check result normal?
Go to Step 26
.
Repair the wiring harness, IG2 line between the ETACS-ECU connector and the fusible link.
STEP 26. Using scan tool (M.U.T.-III), check data list.
(1) caution | To prevent damage to scan tool (M.U.T.-III), always turn the power supply mode of the engine switch to the OFF position before connecting or disconnecting scan tool (M.U.T.-III). |
Connect scan tool (M.U.T.-III). Refer to "How to connect the Scan Tool (M.U.T.-III)

."
(2) Turn the power supply mode of the engine switch to OFF.
(3) Operate the engine switch to change the power supply mode, and check that the data list display of ETACS-ECU is changed.- When power supply mode is ACC or ON.
| ETACS-ECU data list | Item No. | Item name | Normal condition | 29 | Ignition switch(ACC) | ON |
|
- When power supply mode is ON or START.
| ETACS-ECU data list | Item No. | Item name | Normal condition | 30 | Ignition switch(IG1) | ON |
|
- When power supply mode is ON.
| ETACS-ECU data list | Item No. | Item name | Normal condition | 44 | Ignition switch(IG2) | ON |
|
OK: Normal conditions are displayed for all the items.
Are the check result normal?
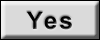
(Normal conditions are displayed for all the items.) :
Go to Step 27
.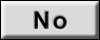
(Normal condition is not displayed for item No. 29.) :
Go to Step 28
.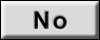
(Normal condition is not displayed for item No. 30.) :
Go to Step 28
.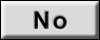
(Normal condition is not displayed for item No. 44.) :
Go to Step 28
.
STEP 27. Recheck for diagnostic trouble code.
Check again if the DTC is stored in the OSS-ECU.(1) Erase the DTC.
(2) Turn the engine switch from "LOCK" (OFF) position to "ON" position.
(3) On completion, check that the DTC is stored again.
Is the DTC stored?
Replace the ETACS-ECU.
Intermittent malfunction is suspected (Refer to GROUP 00, How to Use Troubleshooting/Inspection Service Points - How to Cope with Intermittent Malfunctions
).
STEP 28. Recheck for diagnostic trouble code.
Check again if the DTC is stored in the OSS-ECU.(1) Erase the DTC.
(2) Turn the engine switch from "LOCK" (OFF) position to "ON" position.
(3) On completion, check that the DTC is not stored again.
Is the diagnostic trouble code stored?
Replace the OSS-ECU and register the VIN (Refer to
).
Intermittent malfunction is suspected (Refer to GROUP 00, How to Use Troubleshooting/Inspection Service Points - How to Cope with Intermittent Malfunctions
).