DTC C2204 Internal
abnormality in G and yaw rate sensor
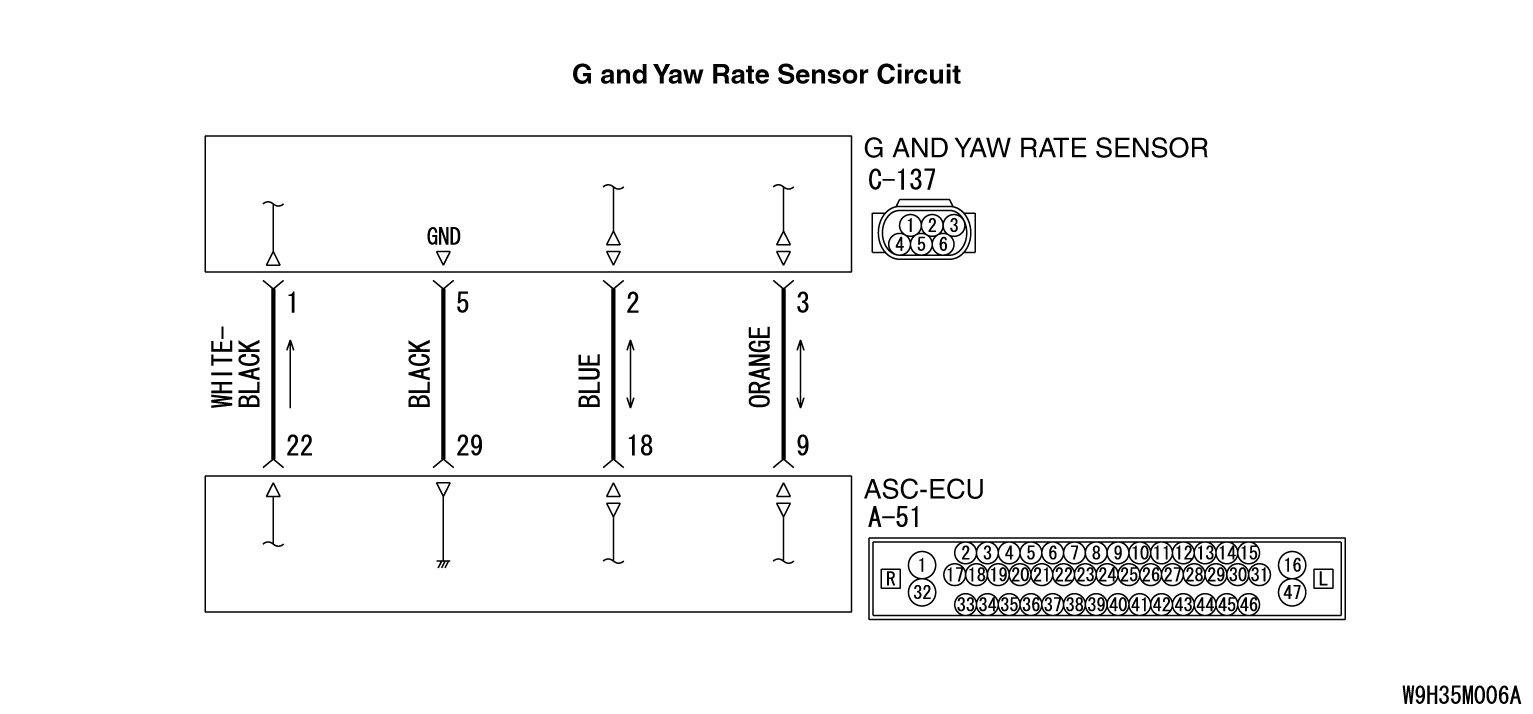
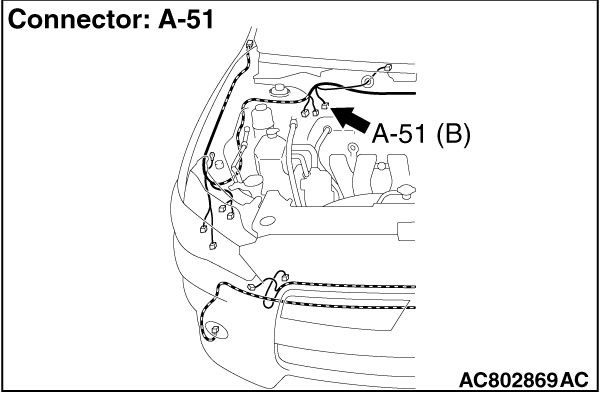
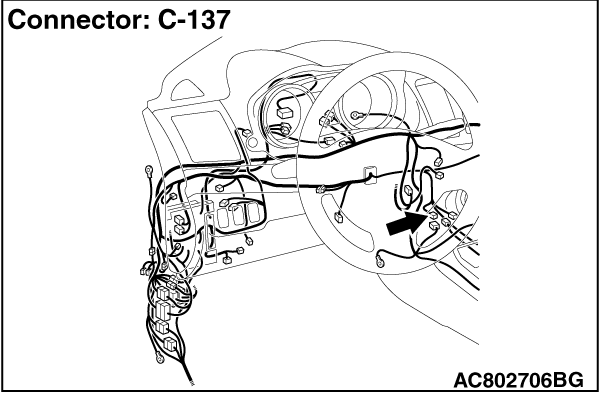
|
caution |
- If there is
any problem in the CAN bus lines, an incorrect DTC may be set. Prior to this diagnosis, diagnose
the CAN bus lines (Refer to GROUP 54C - Diagnostic trouble code diagnosis
).
- Whenever ECU is replaced, ensure that the CAN bus lines are normal.
- Do not drop or shock the G and yaw rate sensor.
- When the G and yaw rate sensor is replaced, always carry out calibration to make
ASC-ECU learn the neutral point (Refer to
).
- When the hydraulic unit (integrated with ASC-ECU) is replaced, always carry out
the calibration of the steering wheel sensor, the G and yaw rate sensor and brake fluid pressure
sensor (Refer to
, and ).
|
|
|
ABS-ECU monitors if the output of G and yaw rate sensor is normal or not.
|
|
This DTC is set if any malfunction below is found:
|
|
- When abnormality is detected by the self-diagnosis of
the lateral G and yaw rate
- When the output value of the lateral G and yaw rate is not within the standard value
range
|
|
note |
This DTC may be set when G and yaw rate sensor is put on the turntable turning at high
speed.
|
|
|
- Wiring harness or connector failure for the special CAN bus lines between
ASC-ECU and the G and yaw rate sensor
- Improper installation of the G and yaw rate sensor
- Damaged wiring harness and connectors
- G and yaw rate sensor malfunction
- ASC-ECU malfunction
|
|
Required Special Tools:
- MB991958: Scan Tool (M.U.T.-III Sub Assembly)
- MB991824: Vehicle Communication Interface (V.C.I.)
- MB991827: M.U.T.-III USB Cable
- MB991910: M.U.T.-III Main Harness A
|
|
STEP 1. Using scan tool MB991958, diagnose the CAN bus lines.
|
|
Use scan tool to diagnose the CAN bus lines.
|
|
Q.
Is the check result normal?
|
|
Go to Step 2.
|
|
|
|
Repair the CAN bus lines (Refer to GROUP 54C - CAN Bus Diagnostic table ).
On completion, go to Step 2.
|
|
|
|
Check that the DTC U0125 is set in ASC-ECU.
|
|
Troubleshoot for the DTC (Refer to ). Then go to
Step 3.
|
|
|
|
Go to Step 3.
|
|
|
|
STEP 3. DTC recheck after resetting CAN bus lines
|
|
Go to Step 4.
|
|
|
|
The procedure is complete.
|
|
|
|
STEP 4. M.U.T.-III data list
|
|
Check the following service data (Refer to ).
|
|
- Item 08: Lateral G-sensor
- Item 09: G-sensor
- Item 12: Yaw rate sensor
|
|
Q.
Is the check result normal?
|
|
Go to Step 8.
|
|
|
|
Go to Step 5.
|
|
|
|
STEP 5. G and yaw rate sensor installation check
|
|
Check that the G and yaw rate sensor is installed correctly.
|
|
Q.
Is the check result normal?
|
|
Go to Step 6.
|
|
|
|
Reinstall the G and yaw rate sensor correctly (Refer to ),
and then go to Step 8.
|
|
|
|
STEP 6. Connector check: A-51 ASC-ECU connector, C-137 G and yaw rate
sensor connector
|
|
Q.
Is the check result normal?
|
|
Go to Step 7.
|
|
|
|
Repair the connector, and then go to Step 8.
|
|
|
|
STEP 7. Wiring harness check between A-51 ASC-ECU connector terminal
No. 18 and C-137 G and yaw rate sensor connector terminal No. 2 as well as between A-51 ASC-ECU
connector terminal No. 19 and C-137 G and yaw rate sensor connector terminal No. 3
|
|
- Check the communication circuit for open and short circuit.
|
|
Q.
Is the check result normal?
|
|
Go to Step 8.
|
|
|
|
Repair the wiring harness, and then go to Step 8.
|
|
|
|
STEP 8. Check whether the DTC is reset.
|
|
(2)Drive the vehicle at 12mph (20 km/h) or higher.
|
|
Replace the G and yaw rate sensor (Refer to ),
and then go to Step 9.
|
|
|
|
Intermittent malfunction (Refer to GROUP 00 - How to Use Troubleshooting/How
to Cope with Intermittent Malfunctions ).
|
|
|
|
STEP 9. Check whether the DTC is reset.
|
|
(2)Drive the vehicle at 12mph (20 km/h) or higher.
|
|
Replace the hydraulic unit (integrated with ASC-ECU) (Refer to ), and
then go to Step 10.
|
|
|
|
Intermittent malfunction (Refer to GROUP 00 - How to Cope with Intermittent
Malfunction ).
|
|
|
|
STEP 10. Check whether the DTC is reset.
|
|
(2)Drive the vehicle at 12mph (20 km/h) or higher.
|
|
Return to Step 1.
|
|
|
|
The procedure is complete.
|
|
|